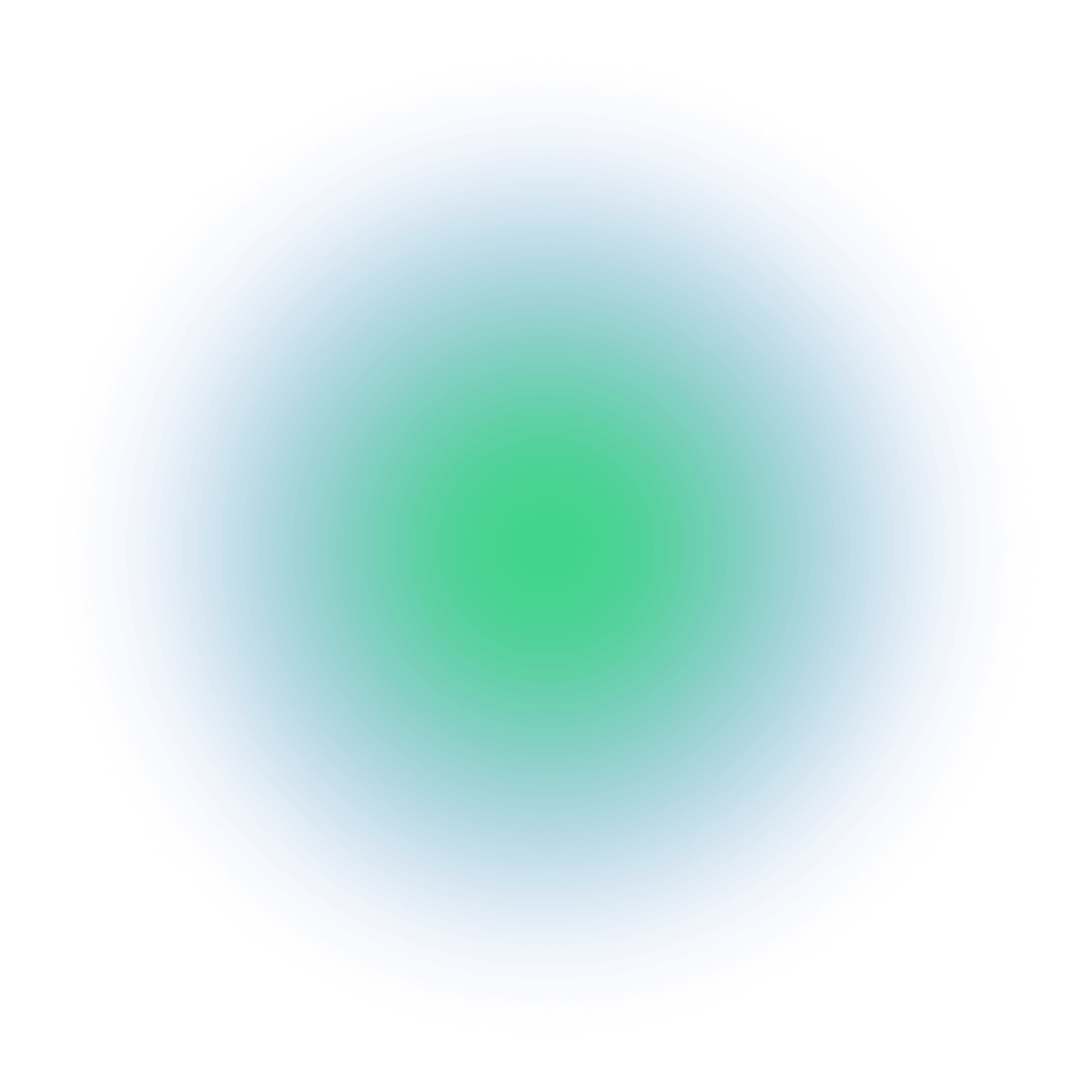
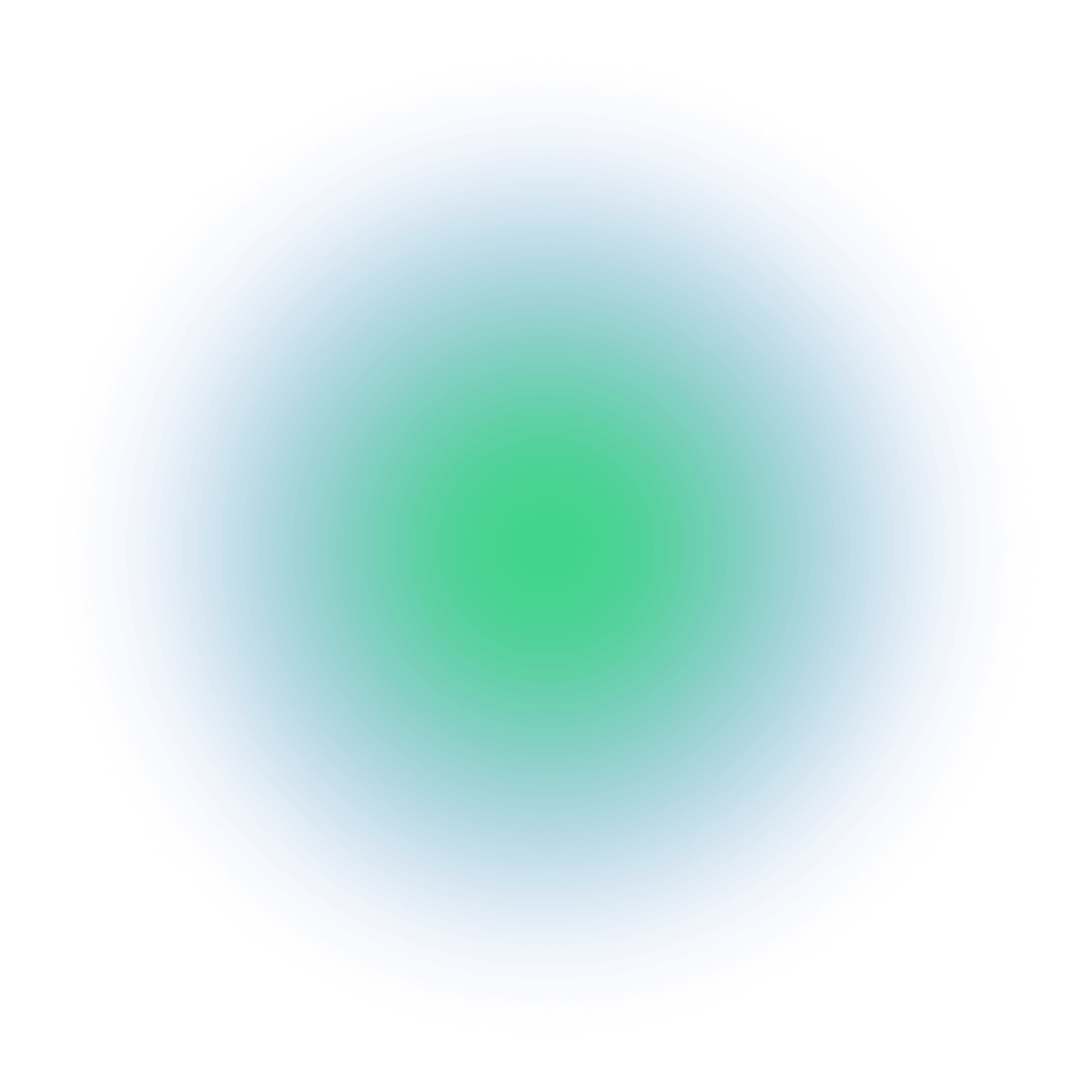
“Uncovering Hidden Savings: How Analysing Utility Bills Helped steel industry to Reduce Costs andBoost Profitability.”
Client
Our client is a leading manufacturer of high-quality stainless steel, nickel alloy, and titanium alloy products. The company has been in operation for over two decades and has established itself as a reliable supplier to a wide range of industries, including aerospace, defence, power, and chemical processing.
With state-of-the-art manufacturing facilities and a team of experienced engineers and technicians, the company is able to provide products of the highest quality that meet the most stringent specifications.
Company has a strong commitment to quality and customer satisfaction. The company’s quality management system is certified to ISO 9001:2015, and its products meet a range of international standards, including ASTM, ASME, and NACE
Goal
Company faced challenges in managing demand and monitoring energy usage due to its large plant and lack of real-time data, leading to high utility costs and penalties. Company also wish to promote sustainability and compliance with regulations, in line with the same company set below goals
- Improve demand management to reduce energy consumption during peak periods.
- Reduce utility costs and avoid penalties for exceeding contracted energy usage.
- Identify areas of inefficiency in the plant to reduce overall energy consumption.
- Obtain real-time data on electrical and water usage to make more informed decisions and optimize resource allocation.
- Implement automated controls and monitoring systems to reduce human error and ensure consistent performance during peak hours.
- Achieve compliance with relevant energy and environmental regulations and standards.
Challenges
While working towards its goal of lowering overall operational cost through smart factory solutions, the facility has faced several challenges, including:
- Retrofitting legacy equipment and infrastructure with smart technology: The facility has old and outdated equipment and infrastructure that is not compatible with smart technology. Retrofitting these systems required significant investments in time and resource which was not possible.
- Process control and optimization: Being heavy Industry efficient control and optimization of critical equipment can have a significant impact on energy consumption and costs.
- Data integration and synchronization: varied data sources, systems, and applications must needed to be integrated and synchronized to provide real-time data on energy usage.
- Ensuring compatibility with existing systems: The facility needs to ensure that the new smart technology is compatible with its existing systems and equipment. This includes addressing compatibility issues with communication protocols, data storage systems, and software applications.
- Addressing workforce challenges: The facility needs to train its employees to operate and manage the new energy management system effectively. This includes identifying training needs, developing training programs, and providing ongoing support to ensure that employees adopt the new system.
- Addressing cybersecurity risks: Needs to implement appropriate cybersecurity measures to protect its data and systems from cyber threats.
Methodology
The implementation of the advanced energy management system was carried out with a strategic and systematic approach as below.
- To overcome the challenge of retrofitting legacy equipment and infrastructure with smart technology, we implemented a system that utilizes software and interfaces to integrate with existing equipment and infrastructure. We also utilized state-of-the-art hardware solutions that do not require extensive retrofitting.
- Deploy advanced process control (APC) solutions to optimize and stabilize processes and minimize energy consumption. This includes using real-time data to predict and prevent operational issues, as well as implementing feedback control systems that can adjust process parameters in real-time for greater efficiency
- We implemented a centralized data management system to integrate and synchronize varied data sources, systems, and applications in real-time by selecting appropriate software solutions and protocols that enabled seamless data exchange and communication between different systems.
- we Provided comprehensive training and ongoing support to employees to effectively operate and manage the new system.
- Firewalls, access controls, and encryption for captured data is implemented to arrest any cybersecurity threat
- The system implementation involves the deployment of approximately 900+ sensors, 75+ processes/equipment, 10+ process controllers ,and 30 data aggregator devices
Result
Achieved utility cost savings by USD 12K/Month by avoiding heavy penalties & availing incentives
Achieved Energy Savings worth 25K USD in first 6 weeks of implementation
Improved power quality resulting 10% equipment failure