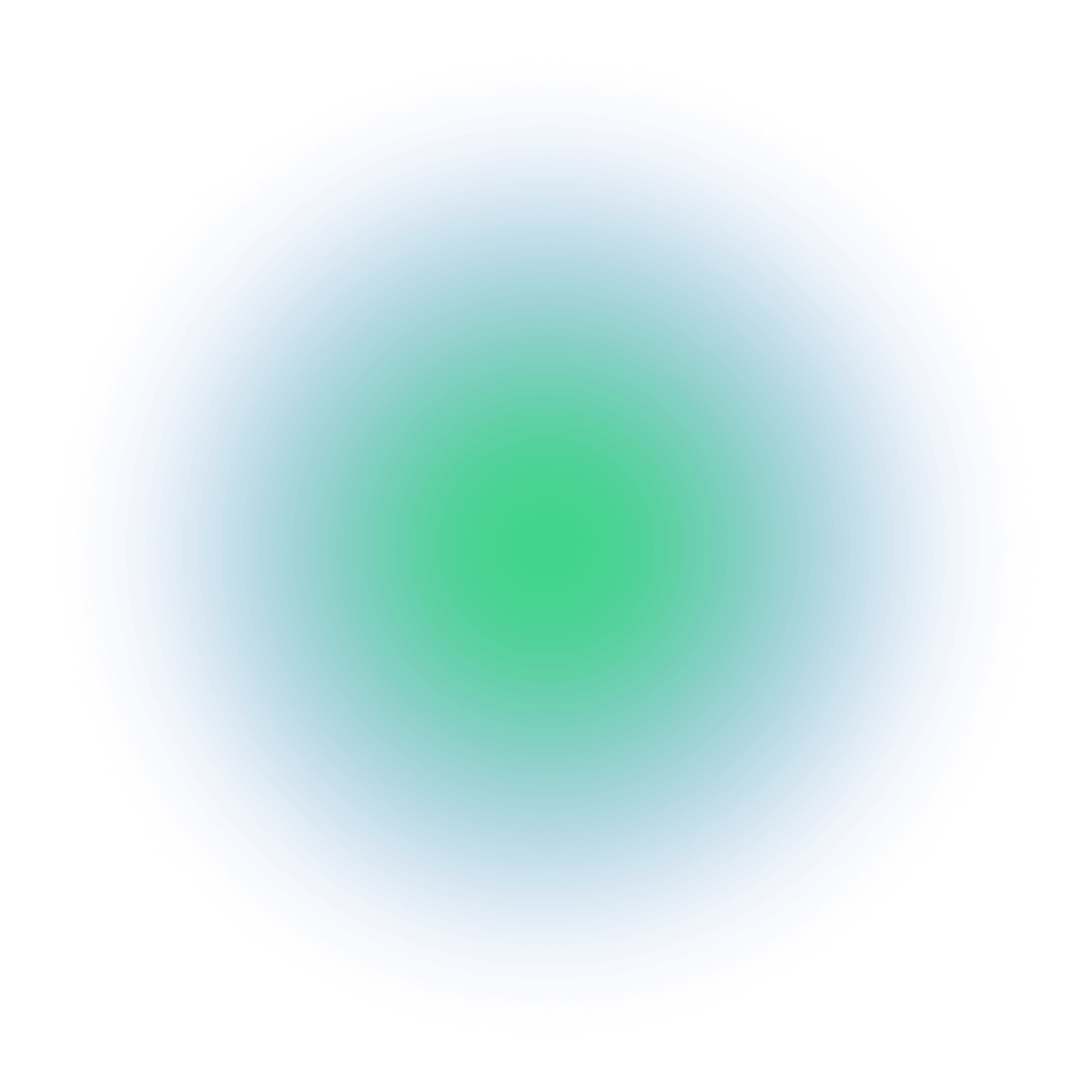
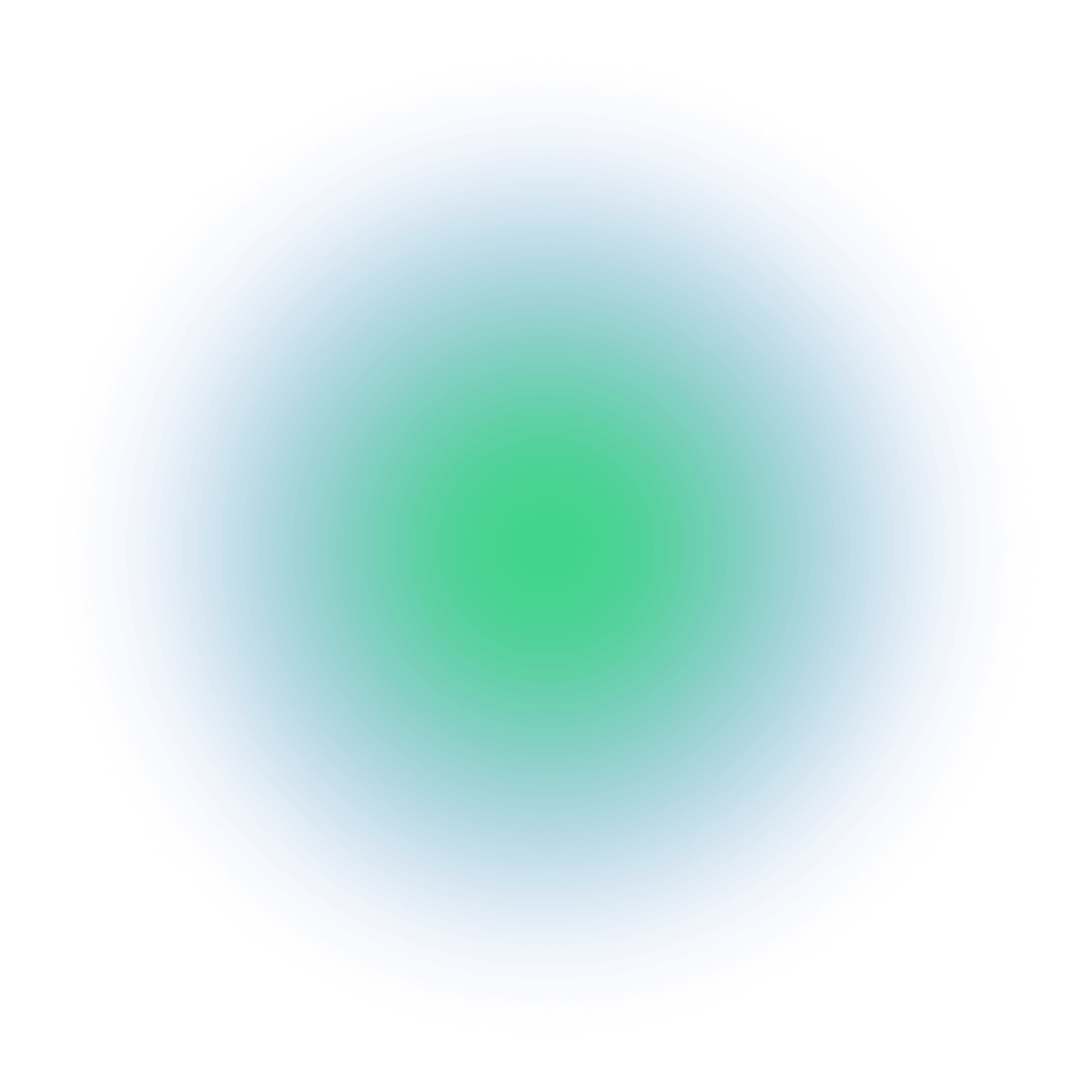
Smart Factory Solutions: Revolutionizing Sustainability and Efficiency in the Paint Industry
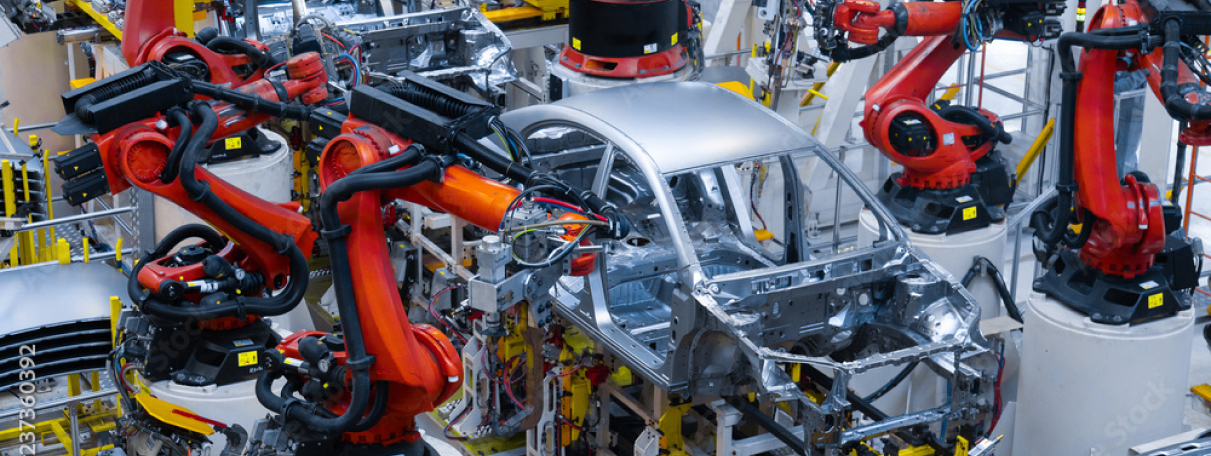
A leading global supplier of high-performance coatings, providing protection and decoration to various industries and sectors, including shipping, offshore, energy, infrastructure, and commercial buildings. With a strong focus on innovation, sustainability, and quality, group offers a broad portfolio of paints and coatings that cater to different needs, from corrosion protection and fire resistance to colour and gloss retention and has over 10,000+ employees worldwide.
Global presence, with operations in over 100 countries. The company has 63 production facilities across 45 countries, including Norway, China, Singapore, the United States, and Saudi Arabia. These facilities manufacture a wide range of coatings, such as marine coatings, protective coatings, and decorative paints, to cater to the diverse needs of different markets.
In addition to production facilities, company has sales depots, offices, and technical service centres in various locations worldwide. This allows the company to provide customers with local support, technical expertise, and fast delivery of products.
Goal
As a responsible player in the paint industry, company is committed to sustainable practices that reduce environmental impact, improve productivity, and enhance customer experience. and have set key goals to guide the efforts.
- Digital excellence program: By Leveraging data analytics and machine learning technologies, integrate energy-efficient technologies, optimizing production processes, and reducing waste and emissions.
- Energy Conservation & Emission cut: The Company aims to reduce its energy consumption and greenhouse gas emissions by 50% by 2030, compared to 2019 levels.
- Improve Productivity: The company aims to increase its productivity by 15% by 2023, through the use of automation, digitalization, and other process improvements.
- Baseline & Benchmarking: Establishing baselines and benchmarks for our products across different manufacturing facilities to identify areas for improvement and implement best practices for sustainability and efficiency for facilities worldwide.
- Committing to alternative energy sources: The Company is committed to using renewable energy sources, such as wind and solar power, and has set a goal to use 25% renewable energy in its operations by 2025.
- Effective water management: The company is also wished to reduce its water consumption.
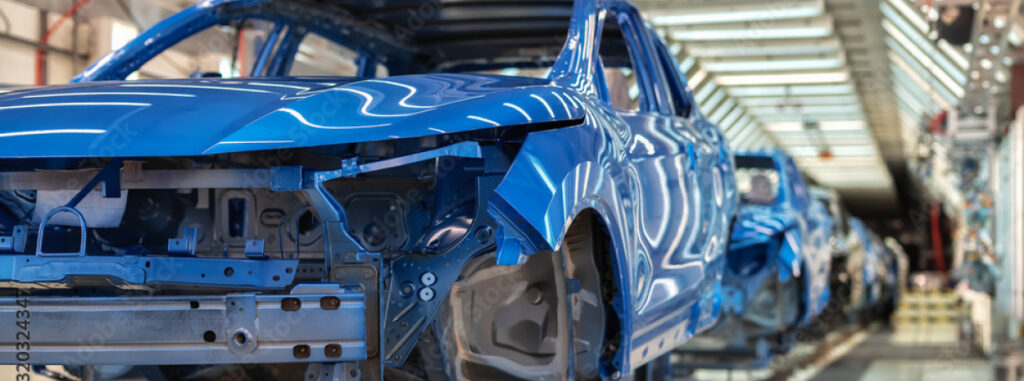
Challenges
While working towards its goal of lowering overall operational cost through smart factory solutions, the facility has faced several challenges, including:
- Developing a Comprehensive Plan for Data Collection, Management, and Analysis: The plant needs a clear plan for how to collect, manage, and use data to make informed decisions about energy use.
- Variations in the existing infrastructure and equipment across different manufacturing facilities, which may require different sensors, equipment, or software systems to be integrated into proposed system.
- Differences in the data acquisition and communication protocols, network infrastructure, and cybersecurity requirements across different geographic regions, which required additional software and communication interface.
- Ensuring data accuracy and completeness from sensors and operators
- Standardization of processes and data across different manufacturing facilities with varying levels of automation and digitization
- Data security and privacy concerns in the transmission and storage of data
- Resistance from floor employees to adopt new processes and technology.
- Adequate Training and Capacity Building of Internal Personnel: The facility needs to make sure that its employees have the skills and knowledge to operate and manage the new systems effectively.
- Measuring ROI Achieved through Implementation: The plant must measure the actual opex savings it achieves through the implementation of smart factory solutions and regularly monitor the system to ensure that it continues to perform effectively.
Methodology
The implementation of the advanced smart factory system was carried out with a strategic and systematic approach as below:
- Connect sensors and equipment to wireless IoT edge devices for capturing energy & process data and transmitting it to a central server.
- Deploy a user-friendly, cloud-based system that allows process and product owners to efficiently and accurately input production plans into a centralized database, which can then be accessed and utilized by the various departments involved in the manufacturing process
- Install handheld devices on each process line to enable operators to access plan and enter real-time process data during execution.
- Develop comprehensive dashboard for Process supervisors to provides real-time visibility into batch processing, machine status, operator performance, shift-wise productivity, cycle time, and equipment utilization.
- Configure a centralized server to aggregate and process data from various data sources, including SAP, ERP, DCS, and equipment HMI.
- Utilizing cutting-edge technologies such as artificial intelligence, machine learning, and incorporating advanced features such as real-time analytics, predictive modelling, and process specifical algorithms to identify areas for improvement for energy & productivity.
- Conduct regular system audits to enhance system efficiency and performance. Utilize advanced data analytics tools to extract valuable insights from large volumes of data generated by the system and use this information to refine and optimize the insights and predictions!
- The system implementation involves the deployment of approximately 1200+ sensors, 160+ processes/equipment, 70 data aggregator devices, 55 handheld devices on process lines
Reults
15% reduction in energy consumption and waste generation, resulting in annual cost savings of $500,000
20% improvement in operational efficiency and equipment utilization, reducing downtime by 2 hours per week and resulting in annual cost savings of $350,000
Improved regulatory compliance and avoidance of $50,000 in potential fines
Enhanced reputation and customer satisfaction, with a 5% increase in customer retention and $1 million in new business opportunities.
About Greenovative
At Greenovative we help organizations achieve operational sustainability through improved energy efficiency, productivity, Safety & reliability.
It uses cutting-edge AI and machine learning technology to deliver tangible results for its clients. Greenovative is dedicated to assisting organizations of all sizes in reaching their operational efficiency goals and optimizing their productivity.