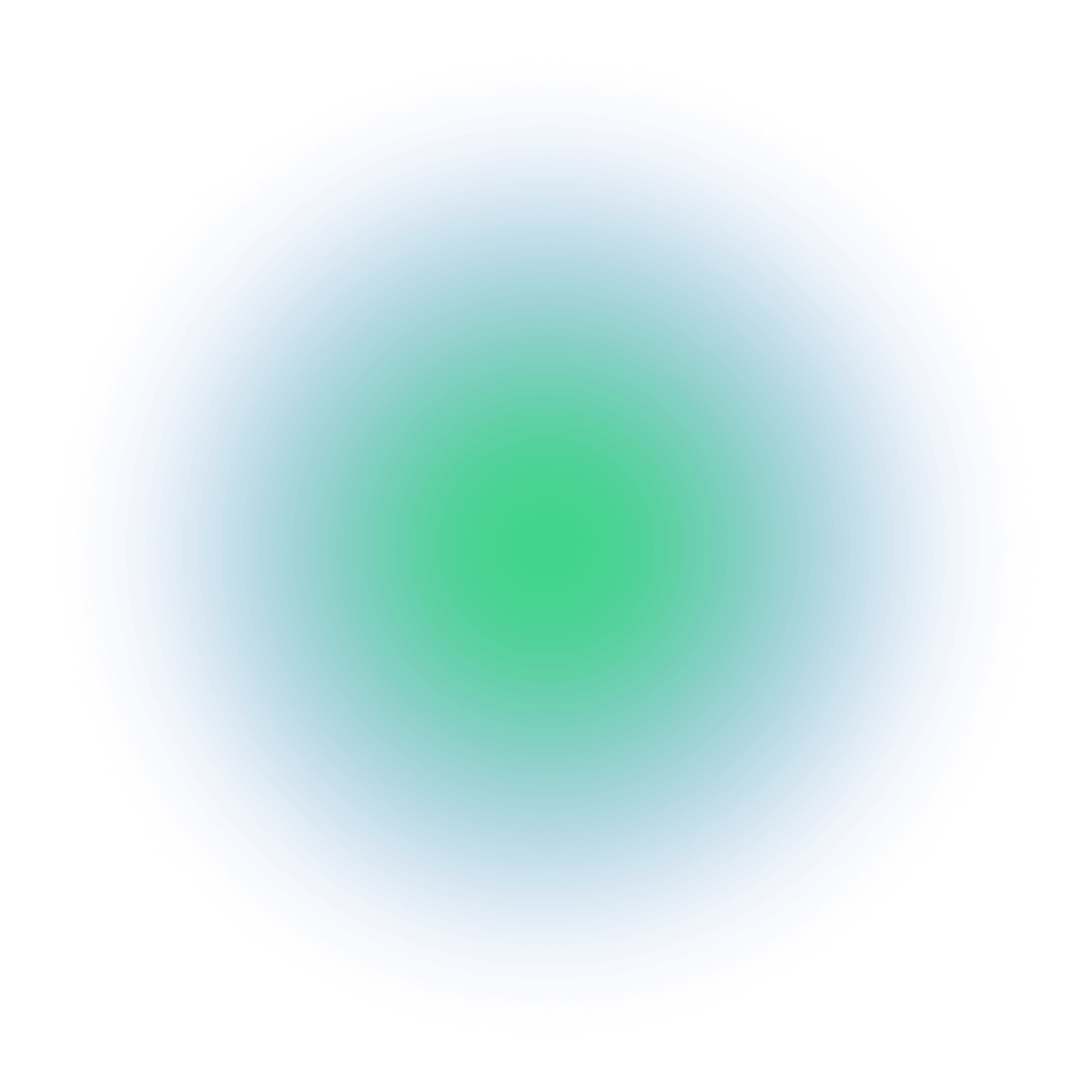
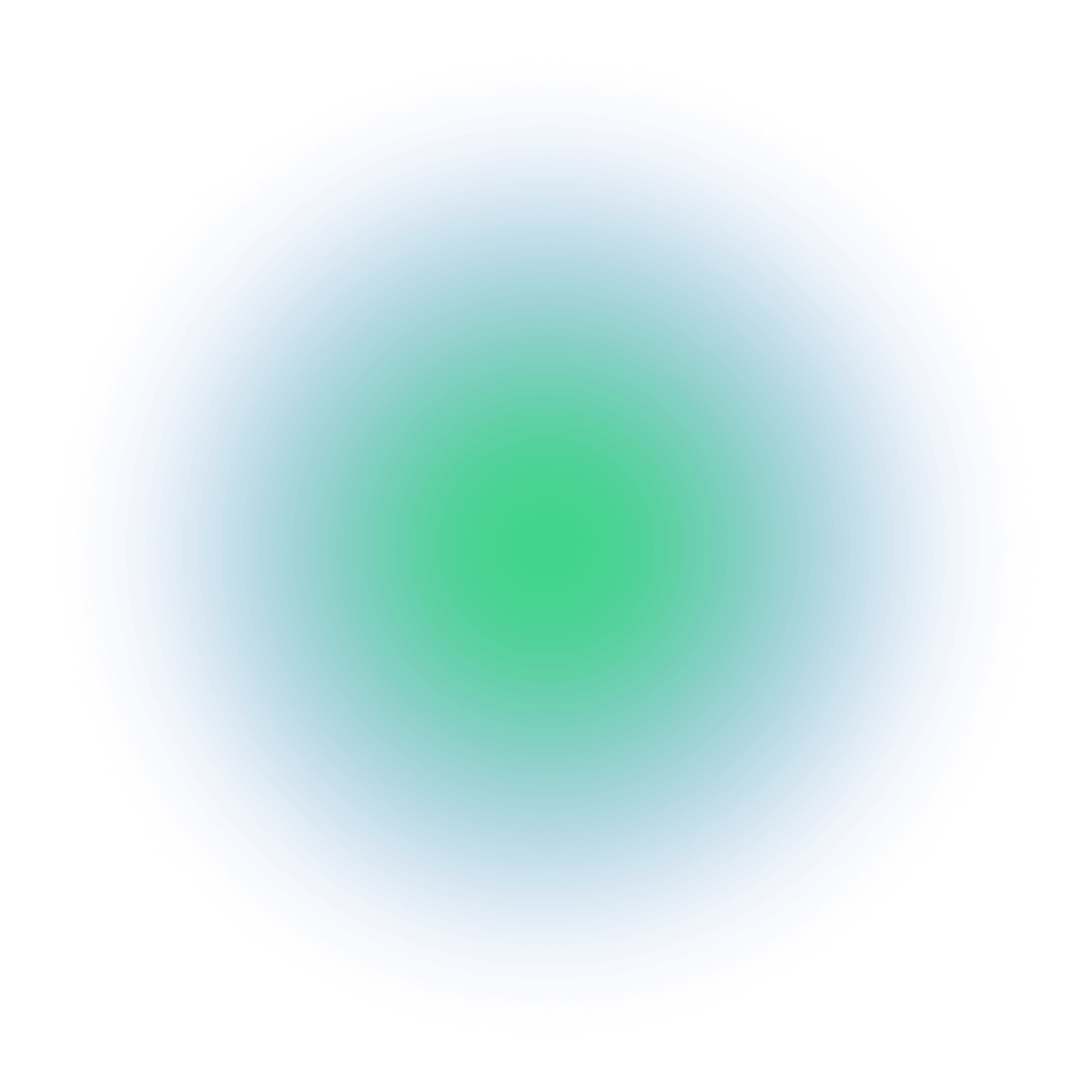
Impact of industrial revolution 4.0 on manufacturing: What will change?
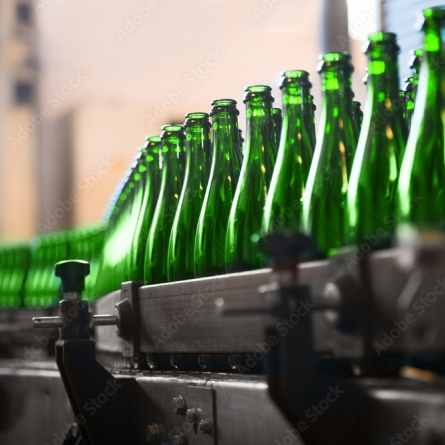
Industry 4.0, also known as the Fourth Industrial Revolution, is a new era of industrial production that is being driven by advancements in digital technology. The Fourth Industrial Revolution is characterized by a fusion of technologies such as the Internet of Things (IoT), artificial intelligence (AI), robotics, and the cloud, among others. Industry 4.0 is changing the way manufacturing is done, bringing new levels of automation, efficiency, and flexibility to the production process.
So, what will change in the manufacturing industry as a result of Industry 4.0? Let’s take a closer look:
- Smart factories: Factories will become more connected, allowing for real-time data collection and analysis, as well as remote monitoring and control of production processes. This will enable manufacturers to quickly respond to changes in demand and adjust production processes in real-time.
- Data-driven decision making: The availability of real-time data from connected devices and systems will enable process owners to make more informed decisions, leading to increased efficiency and improved productivity.
- Increased Automation – One of the key changes that Industry 4.0 will bring to manufacturing is increased automation. With advancements in robotics, AI, and other digital technologies, more and more tasks can be automated, freeing up workers to focus on higher-value tasks. This will increase production efficiency and reduce the need for manual labor.
- Improved Flexibility – Industry 4.0 technologies, such as IoT and the cloud, will allow for greater flexibility in production. For example, with real-time data from sensors and connected devices, manufacturers can quickly respond to changes in demand and adjust production accordingly. This will enable them to be more responsive to market needs and to better meet the needs of their customers.
- Better Quality Control – Industry 4.0 technologies, such as predictive maintenance and AI-powered quality control, will help manufacturers achieve higher levels of quality control. Predictive maintenance, for example, will allow manufacturers to identify potential issues before they become problems, reducing the need for unscheduled downtime and improving overall quality control.
- Increased Efficiency – With Industry 4.0, manufacturers will be able to optimize their production processes, reducing waste and increasing efficiency. For example, sensors and IoT devices can provide real-time data on energy consumption, allowing manufacturers to optimize their energy use and reduce costs. Additionally, advanced analytics and machine learning algorithms can help manufacturers identify areas for improvement and make data-driven decisions.
- New Business Models – Industry 4.0 will also bring about new business models, as manufacturers look for new ways to differentiate themselves in a competitive marketplace. For example, manufacturers may start offering new services, such as predictive maintenance or predictive supply chain management, to better meet the needs of their customers.
- Reshoring of manufacturing: The increasing automation of manufacturing processes will make it possible to bring production back to countries where it was previously outsourced, leading to increased employment opportunities and economic growth.
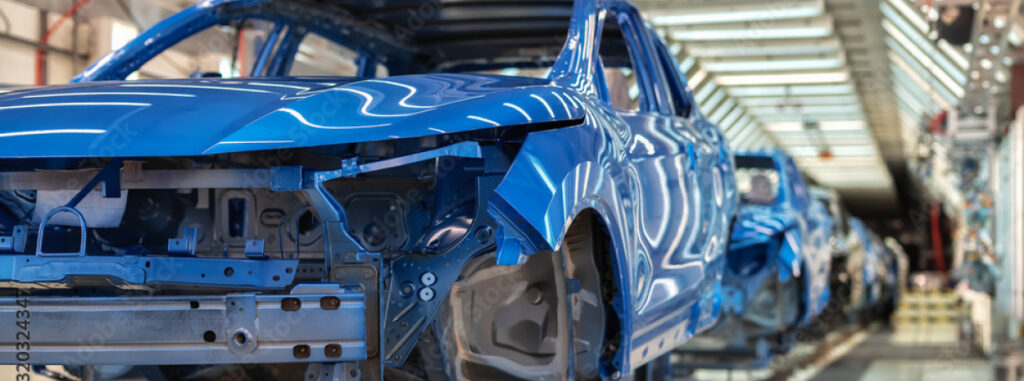
In conclusion, Industry 4.0 is set to bring about major changes to the manufacturing industry. With increased automation, improved flexibility, better quality control, increased efficiency, and new business models, manufacturers will be well-positioned to meet the challenges of a rapidly changing market.
By embracing Industry 4.0, manufacturers will be able to stay ahead of the curve and stay competitive in a rapidly changing market. Whether you’re a small manufacturer or a large multinational corporation, it’s never too late to start thinking about how Industry 4.0 can help you transform your business and stay ahead of the curve.