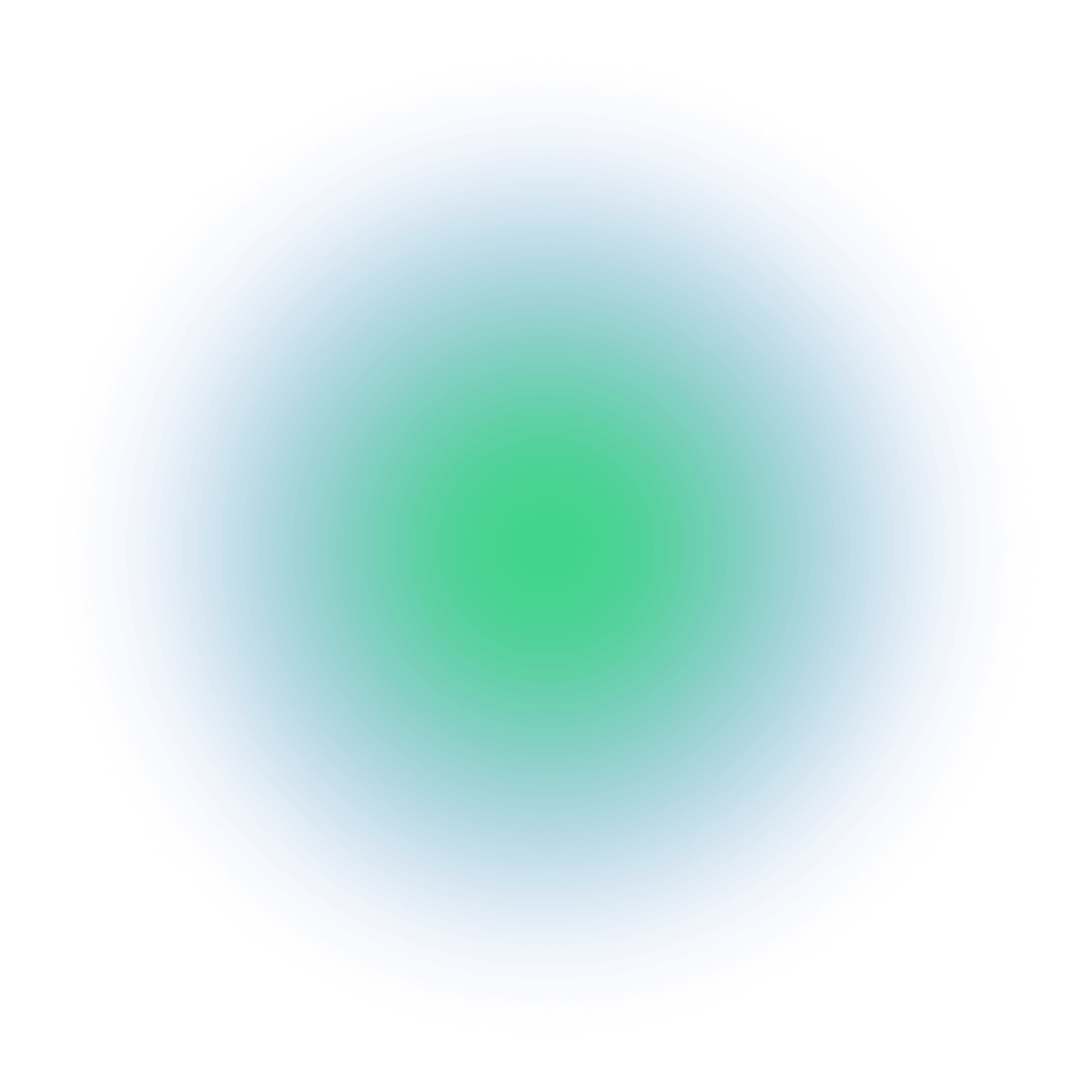
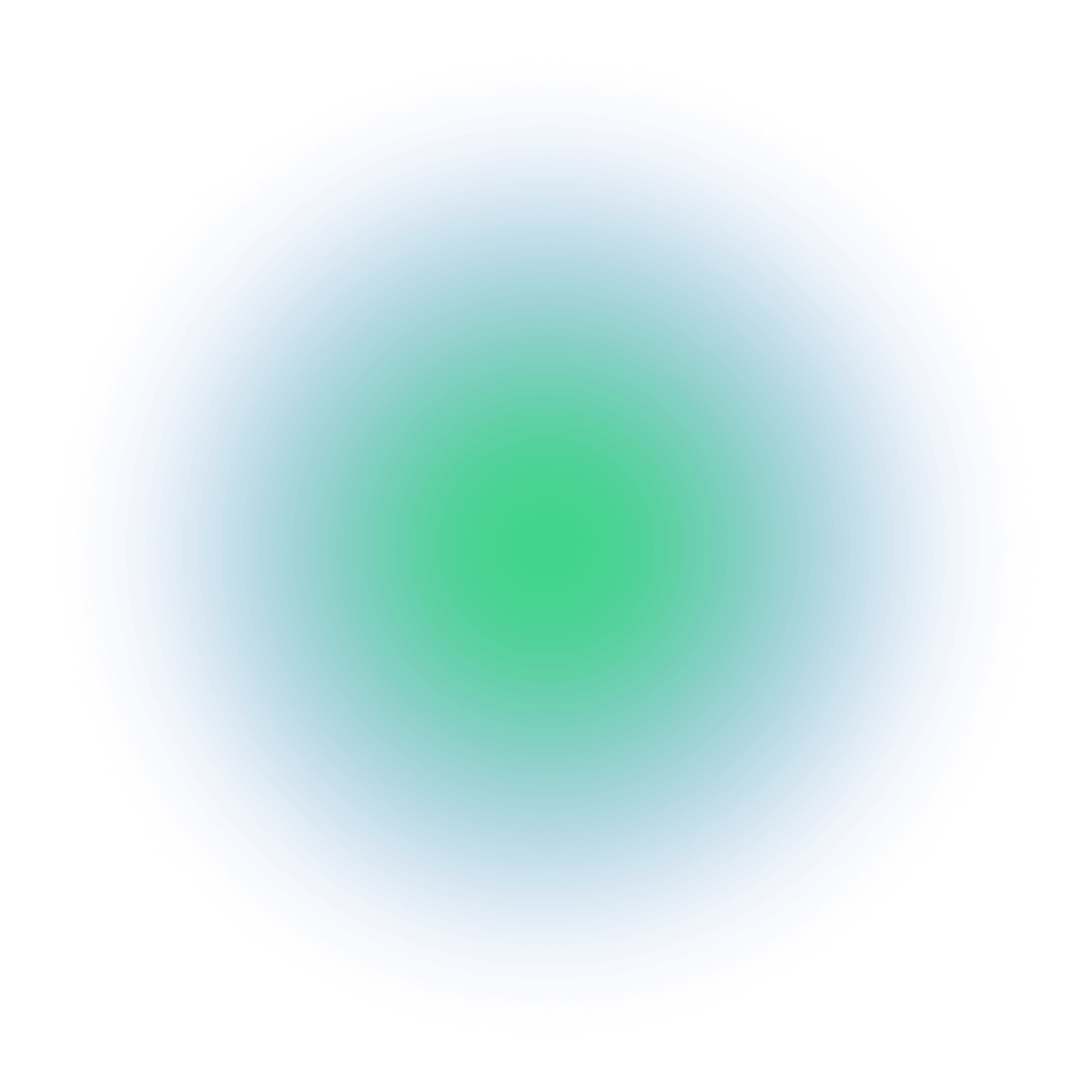
Driving Energy Efficiency and Sustainability: A Digital Transformation Success Story for a Multinational Conglomerate Corporation
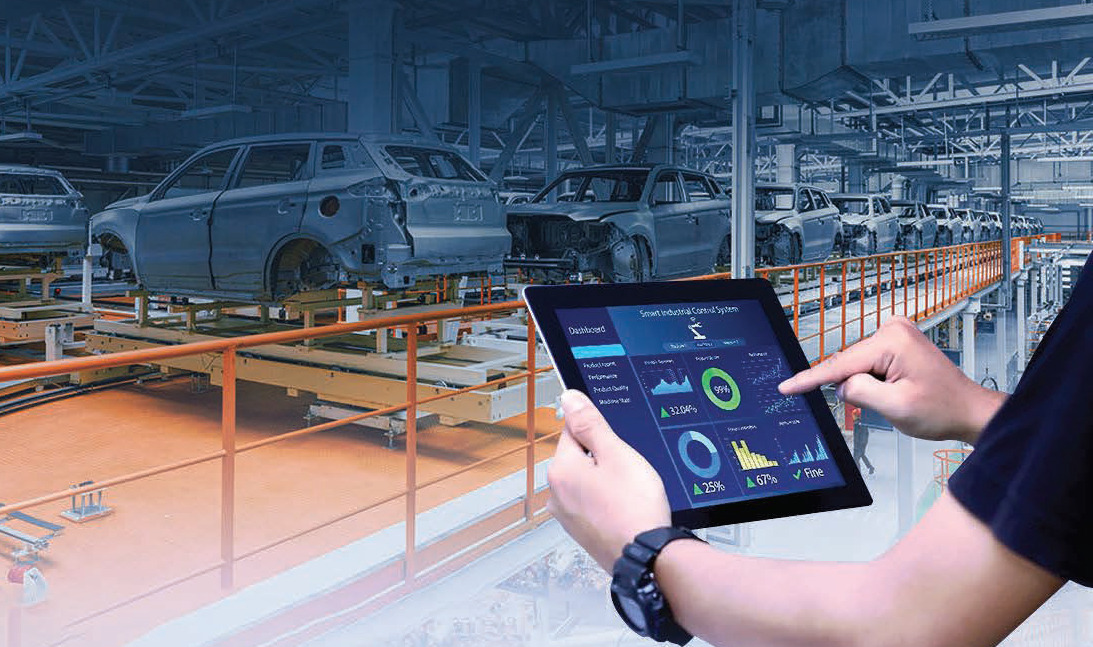
The multinational conglomerate corporation headquartered in Mumbai, India, the company has a long and rich history of providing innovative products and services to customers around the world. With over 120,000 employees and operations in over 36 countries, the Group has established itself as a leader in several industries, including textiles, telecommunications, metals, cement, and financial services. The group’s mission is to deliver superior value to its customers, shareholders, and employees, while also making a positive impact on the communities in which it operates. The Group is committed to sustainability and is known for its ethical and transparent business practices. With its focus on innovation and growth, the Group is well-positioned to continue making a positive impact for generations to come.
Goal
The facility has set several goals with a vision of utilizing digital transformation and cutting-edge technology to drive energy efficiency and operational sustainability.
- Reduce Energy and Water Use: The plant is working to use less energy and water, which can save OPEX cost and improve operational sustainability
- Lower utility bills: facility recognizes the significant impact of utility costs on its overall operation and is focused on reducing these costs.
- Keep Equipment Running Smoothly: To keep production going, the plant is focused on keeping its equipment working properly without any downtime.
- Explore Alternative Energy Sources: The facility is looking into using different types of energy that are more efficient and better for the environment.
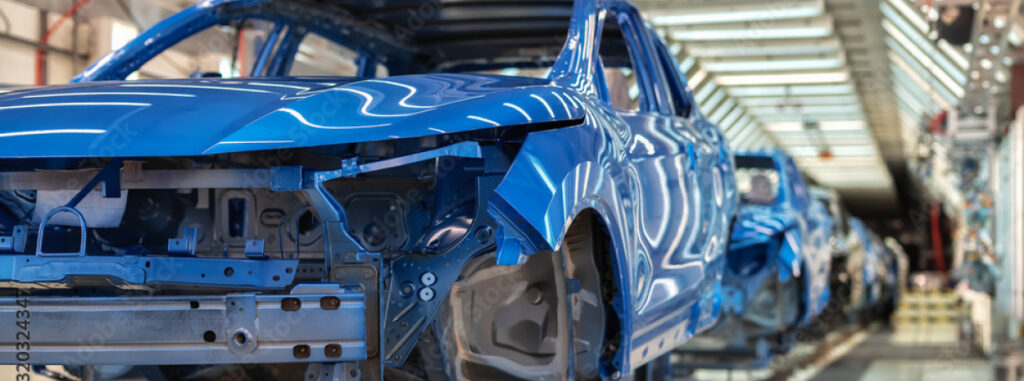
Challenges
While working towards its goal of lowering power costs through digital Transformation, the facility has several implementation challenges, including:
- Developing a Comprehensive Plan for Data Collection, Management, and Analysis: The plant needs a clear plan for how to collect, manage, and use data to make informed decisions about energy and water use.
- Integrating New Hardware and Technology with Existing Legacy Systems: The facility needs to figure out how to add new technology to its existing systems in a way that is efficient and reliable.
- Minimize Capital and Implementation Costs by Integrating Existing Sensors and Processes: The facility aims to integrate its existing sensors and processes into the new smart factory solution, in order to reduce capital and implementation costs while still realizing energy efficiency gains.
- Identifying and Mitigating Risks of Downtime and Service Disruptions: To avoid interruptions in production, the plant must identify and minimize any risks that could cause downtime or service disruptions during the implementation process.
- Adequate Training and Capacity Building of Internal Personnel: The facility needs to make sure that its employees have the skills and knowledge to operate and manage the new systems effectively.
- Measuring Energy Savings Achieved through Implementation: The plant must measure the actual energy savings it achieves through the implementation of smart factory solutions and regularly monitor the system to ensure that it continues to perform effectively.
Methodology
The implementation of the advanced energy management system was carried out with a strategic and systematic approach as below
- Identifying Key Assets and Processes: The facility identified the key assets and processes that were critical for data collection, so that it could focus its efforts on monitoring and capturing data from these areas.
- Checking Sensor Availability: The team checked the availability of sensors at the facility and created templates for each type of sensor to help organize the data. They also identified the data parameters that needed to be captured.
- Testing Communication Systems: The team tested its communication systems and decoded OEM manuals to ensure the data collected from the sensors could be effectively communicated and used for decision making.
- Centralizing Data with Aggregators: The team installed data aggregators to collect and centralize data from existing networks, making it easier to manage and analyze in real-time.
- Integrating Existing Systems: The team integrated existing systems, such as production management systems, OPC servers, SCADA, and DCS, so that data from all sources could be effectively utilized in the new energy management system.
- Verifying and Validating Data: The facility verified and validated the data that was being captured to ensure its accuracy and completeness.
- The energy management system implementation involves the deployment of approximately 1200+ sensors, 115+ processes/equipment, and 70 data aggregator devices.
Result
Achieved energy savings of 8% across the facilities.
The company achieved a 24% increase in machine uptime, thanks to the self-healing system that automatically diagnoses and responds to issues, leading to a 15% increase in system efficiency.
The customized dashboard of the energy intelligence platform enabled the company to identify high-energy consuming machines and measure their efficiency and lifecycle.
About Greenovative
At Greenovative we help organizations achieve operational sustainability through improved energy efficiency, productivity, Safety & reliability.
It uses cutting-edge AI and machine learning technology to deliver tangible results for its clients. Greenovative is dedicated to assisting organizations of all sizes in reaching their operational efficiency goals and optimizing their productivity.
Replaced old motors with more energy-efficient IE 3 motors account almost saving USD 50K /Month